Creating Big Change with Single Ideas
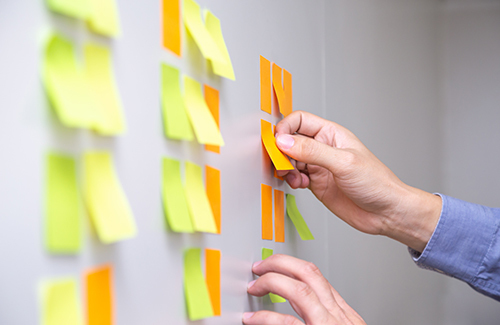
A single idea to improve even the smallest aspect of a task has the power to create a ripple effect to be felt throughout an entire company—and impact all stakeholders in the supply chain. It’s why we are so committed to giving our employees a voice. After all, we hired them for the value they bring through the door every day and rely on them to do their jobs well. They are the experts at their responsibilities and the best source for feedback and input for what works … and what does not. By collecting ideas from hundreds of employees and pairing them with the correct process, we forge a tool to improve employee satisfaction while taking an assertive drive towards true lean manufacturing.
A Model That Works
When pursuing lean manufacturing, the biggest challenge is finding and applying the model and system that will best work for the company and the current situation. Our end goal is to perform as a true lean organization, with employees of all levels learning and solving problems, that in the end, results in continuous improvement. This process started off with a simple recommendation box; but how does an anonymous suggestion result in lean manufacturing improvements? Guided by processes from 6S and the Shingo Business Model, we implemented the “idea board system.”
In 2018, we successfully executed 1,566 solutions to problems that were identified from our 360 employees. Each problem was given equal effort for resolution, regardless of who initiated it. We applied the key components of the Shingo business model to each suggestion: respect and humility.
Building the Process
But Hobson & Motzer did not jump from a recommendation box to having a system that generated 1,566 solved problems overnight; there was a process behind it. It started with the with the expansion of our precision metal stamping and machining plant and the subsequent relocation of our coined wire department. When news of the relocation hit our quality assurance department, we seized the opportunity to completely rebuild with lean manufacturing principles as our guide.
The relocation was thoroughly planned and designed to eliminate waste, and was the first location within Hobson & Motzer with the newly implemented idea board. Once this was executed, the department consistently reported with the highest internal 6S score and was the smoothest running department in the company. We then replicated the system in each department until the entire company was performing the idea board system.
Based on guidelines set by Alan Robinson & Dean Schroeder, authors of Ideas are Free, Hobson & Motzer actively incorporates an idea board system into our daily routine.
The Idea Board System
To ensure a consistent approach to each idea, we follow a process for identifying and addressing each core issue we pursue through the idea board system.
This is how it works:
- After a core reason for a problem is identified, it is noted and addressed during bi-weekly meetings.
- An execution plan for resolution is made.
- Completion date is determined.
- Person accountable for next step towards resolution is identified.
- Every step is tracked and recorded.
- Progress is measured.
Thinking Inside the Box
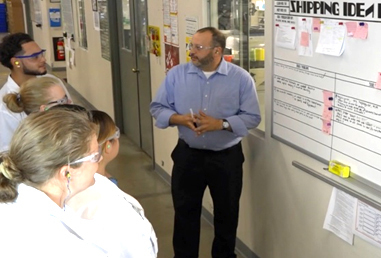
It’s not always the big ideas that make differences, and we realize that new ideas for improvement are not always easy to find. If you walk into our plant with the intention of finding an issue, odds are you will return empty handed. To continuously improve upon ourselves, it is essential to always change our thought process, and take note of the slightest inconvenience. Sometimes thinking inside the box is the best approach.
The implementation of the idea board produces:
- Happier employees
- Collaborative perspective
- Lower costs
- Optimized time management—less wasted time
- Streamlined processes
- Cohesive work culture
- Continuous improvement
The strength and reach of any organization is as good as its weakest link and limited vision. We have found this idea board system to provide a type of cultural glue to fortify us as a cohesive, collaborative force—internally and externally—that shares a common goal of exploring what is possible. This affects everything we do as a precision metal machining, stamping, and assembly provider and translates to our ability to produce and deliver consistent, top-quality precision metal parts and components to our customers. The idea board system has created immense benefits to us. What can it do for you?